Prototyping in Industrial Design
Industrial design prototyping can be seen as a bridge between the initial concept design stage and the production stage of manufacturing. Prototyping will progress iteratively in conjunction with product design to ensure that the development process continues to perform as designed and intended.
- Home
- Industries
- Prototyping in Industrial Design
What Is Industrial Design Prototyping?
As the pace of product design for industry increases, designers are pushing ahead with the bridge between concept and production in the fastest time possible. Industrial design prototyping is the first step in putting ideas and concepts in product design into practice, exploring solutions for product design manufacturability by moving designs into production-ready prototypes. Product design prototyping involves applications such as proof of concept, visual presentation, functional testing, engineering and production validation, and accurately communicates design intent, functional usability, material feasibility, and the working mechanism and performance of the product to manufacturers and product engineers.
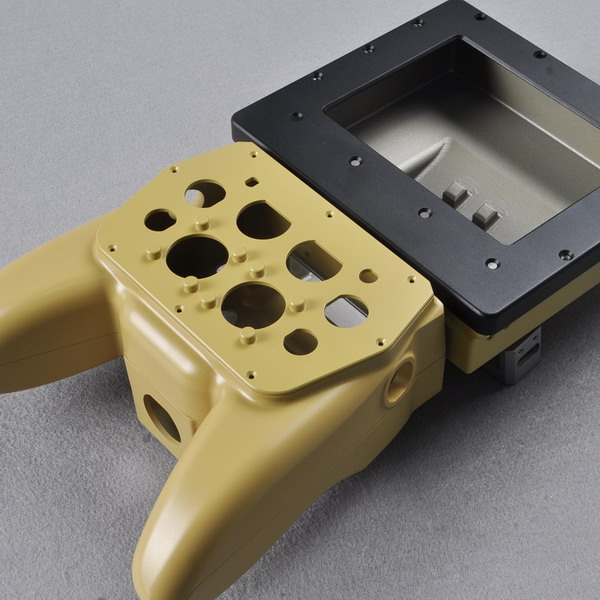
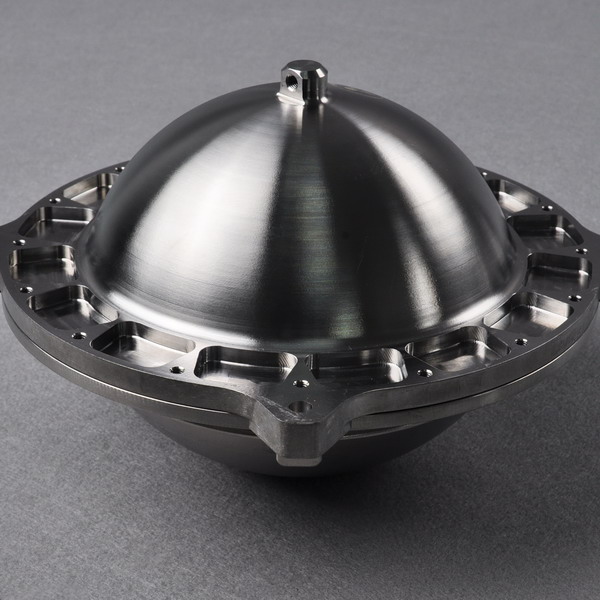
Why Prototyping is Essential to Good Product Design?
Good product design should always focus on the end user first and foremost to ensure that they get the best experience with the product. Prototype design could be anything from a simple part file to models of complex assembled parts. There is nothing that brings you closer to the functionality of the final product faster than prototyping.
Based on this, seasoned designers always transition between concept design, CAD modeling, and prototyping to validate their ideas. This back and forth conversation between design and prototype creates an iterative process in which each tool reveals new opportunities and problems to explore and further refine.
For industrial designers, product design prototyping is always a crucial step within the creative process to help you better understand the user experience. This works both externally – presenting to clients and stakeholders – and internally – in collaborating more deeply with your team, or rallying them to support a new idea.
Get Help from Prototyping Experts for Your Industrial Design
During the product design process, it’s a good idea to seek professional help from a company with proven experience in prototyping and manufacturing. Work with prototype technology experts to find solutions for complex processes such as machining, molding, finishing and surface treatment, test and evaluate the viability of designs, identify potential problems and make improvements.
WayKen is a leading rapid manufacturer specializing in rapid prototyping and low volume manufacturing of plastic and metal parts, providing a one-stop shop from prototype to production. We have the capability and expertise to meet all your stringent design needs, helping you test, evaluate and improve to prove and refine your product design.
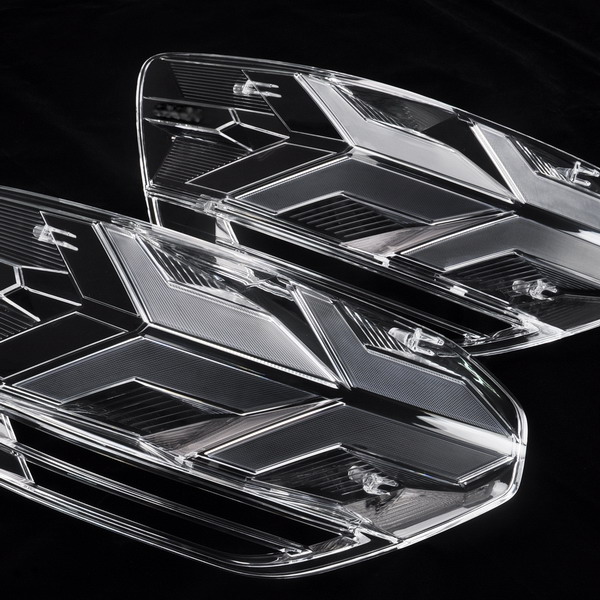
Prototyping will Bring Your Designs to Life
From the initial concept prototype and visual presentation models to complex design functional prototypes, as well as challenging precision machined parts, we are able to support at all levels.
The Application and Advantages of Prototyping In Industrial Design
Industrial design prototyping helps teams collaborate better with each other, identify and solve problems early, and improve existing designs. These applications and advantages are well worth the extra time and effort.
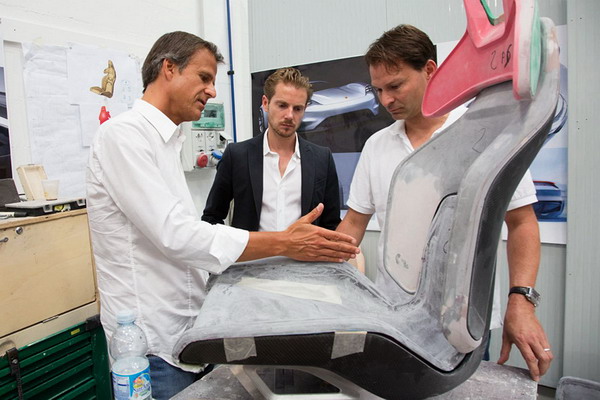
Design Discussion
It is very important to discuss during product designing. Visualization is a significant part for design expression, and it is also the basic for design discussion. During design idea generation stage, from initial 2D sketch design expression to later detail discussion, prototypes will act as a specified discussing object that makes the detail more clear and the visual more real. Obviously it has irreplaceable advantage in communication and collaboration of the entire team.
Design Optimization
On the one hand, prototypes visualize the design, identify design problems in time and collect feedback, and then optimize the design for the rapid iteration of the product design. On the other hand, reverse engineering techniques are used to scan the prototype to get 3D model data to get arguments and refine the design. In this process, prototyping is used for visual evaluation to ensure the overall look and feel, and design efficiency is greatly improved.
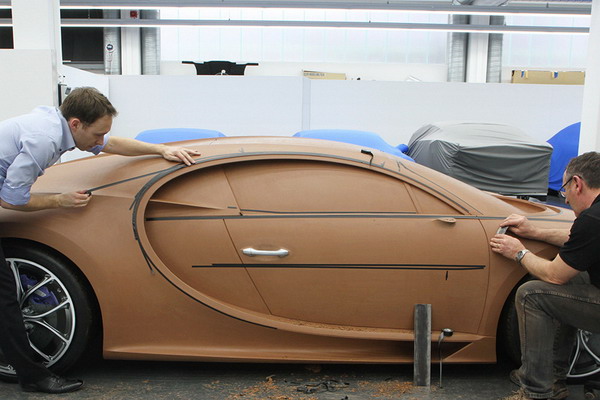
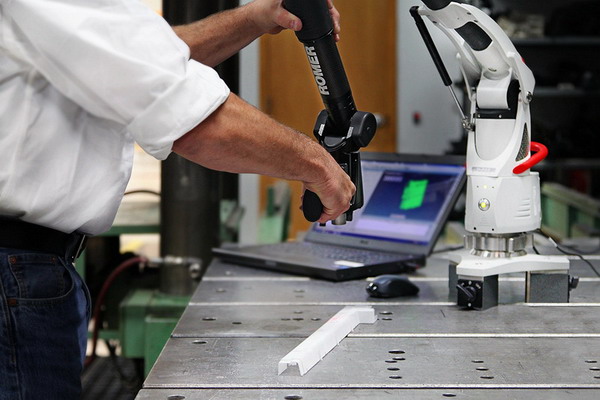
Design Testing
The purpose of design testing is to get quick feedback on the usability of a product design prototype. In general, you need to build accurate functional prototypes for the test and evaluation process. With a series of working scenario tests for form, fit and function that help evaluate materials, strength, tolerances, assemblies, usage functions, working mechanisms and potential costs, it will ensure that your design meets the expected specifications and manufacturability.
Design Verification
Prototyping and manufacturing later in the product design phase is a critical step in engineering and design verification, helping you to extend proof-of-concept models to high-quality engineering prototypes and pre-production samples that simulate the final product. This phase of testing will verify that the design meets expected product performance, certification standards, manufacturing processes and production schedules, guiding subsequent mass production through a series of verification phases.
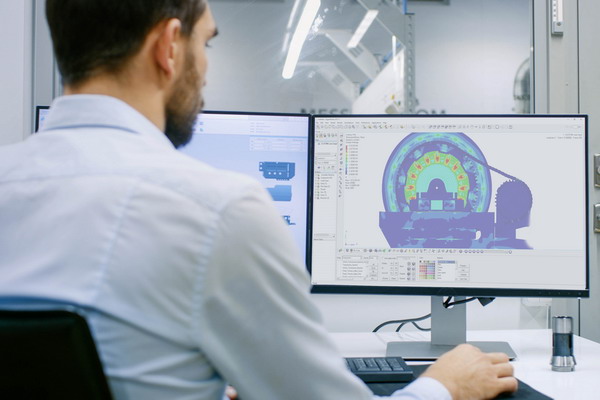
You Design It We Will Manufacture It For You
Make Your Ideas Into Products